
CASE STUDY
導入事例
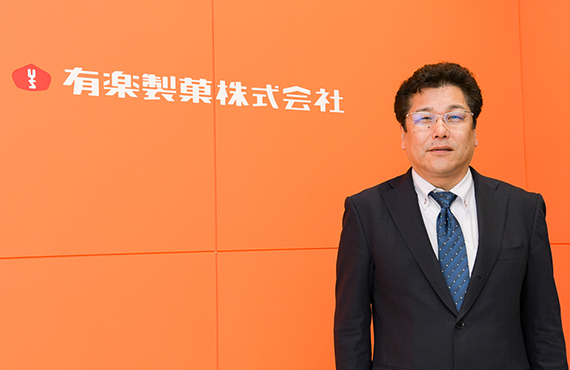
YURAKU CONFECTIONERY CO.,LTD.
Toyohashi Dream Factory
Low fuel consumption and high quality service were our deciding factors.
Consciously contributing to energy-saving production lines
Yuraku Confectionery Co., Ltd. is famous for its chocolate bar, called the Black Thunder. Two Naigai Vicars' ovens are currently being used at the Toyohashi Dream Factory. An interview of Mr. Takahashi, Director of Production Engineering Division, was held to learn what were the key factors that led to the implementation of Naigai Vicars’ ovens.
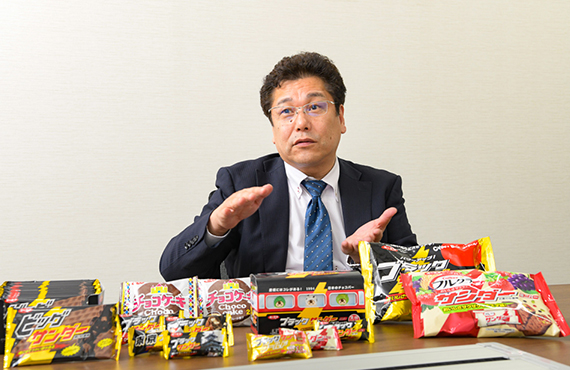
Based on previous successful results, two Naigai Vicars' ovens were installed at our Toyohashi Dream Factory.
Q: What are the main products of Toyohashi Dream Factory?
A: Starting with the Black Thunder, the main products of Yuraku Confectionery Co., Ltd. are a combination of baked sweets with chocolate. For example, some cookies are chocolate-covered, while others are chocolate-covered sponge cake products called, Choco Cake.
Q: There are many existing fans of Black Thunder and Choco Cake, aren’t there?
A: Thank you. In addition to periodic media coverage and exposure of Black Thunder, our Choco Cake products have been manufactured for over 20 years by Naigai Vicars, thankfully generating many fans.
Q: What was the catalyst or genesis to start using Naigai Vicars' ovens?
A: Actually, we have been enjoying a fruitful relationship with Naigai Vicars for more than 40 years. Based on the reliable maintenance service and quality products that can be produced with Naigai Vicars’ ovens, when we decided to construct the Toyohashi Dream Factory, we selected Naigai Vicars' ovens for two of the three confectionery lines.
Q: How would you rate the usability of Naigai Vicars' ovens?
A: Thanks to the improved energy efficiencies and baking capabilities, we have been very pleased and glad to have chosen to install two Naigai Vicars’ ovens. We have been using the existing ovens for 7 to 8 years, and they are very good.
Furthermore, we are confident and can trust the quality and reliability of Naigai Vicars’ Japanese-made equipment.
Q: Your factory also has foreign-made ovens. What are the differences between Japanese versus overseas manufacturers?
A:There are many differences.
Overseas manufacturers often provide a full production line-up, from molding to oven as equipment as a package. Since biscuits are originally from overseas, this is understandable and natural. If one plans to have a Japanese made production line, for example, it is necessary to separately add a molding machine to a Naigai Vicars' oven. Consequently, an overseas manufacturer can offer a production line at a cheaper initial cost.
On the other hand, a major or significant disadvantage of overseas manufacturers is their maintenance service, or lack there of. Starting with difficulties in procuring parts, a confectionery maker should recognize and account for these hidden costs and risks at the purchasing stage. As an example, it can take one month of delivery for just a single screw.
If you want to build a versatile production line, Japanese manufacturers are the best. Once you have a molding machine selected, there is no doubt in our minds that the oven we would choose would be a Naigai Vicars' oven. We have overwhelming confidence in their reliability and quality and feel that this would be a very safe decision.
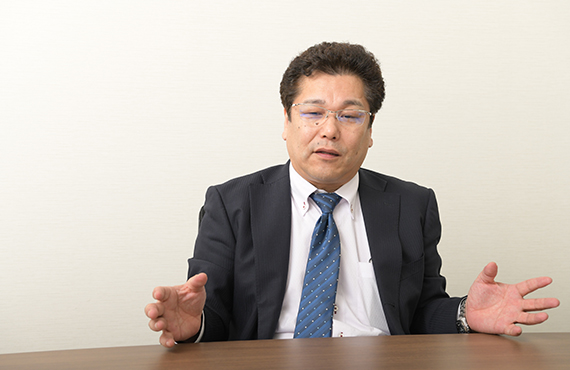
Customization request for enhanced thermal insulation
Q: Please give us a brief description of your existing two Naigai Vicars’ ovens.
A: While the lengths are both 25meters, the width of one oven is 800mm wide and the other is 1000mm wide. Both are Direct Gas-Fired ovens and use steel bands. While there are various baking methods, Naigai Vicars' ovens have unique burners. They provide excellent heat efficiency and low energy usage; in other words, low fuel consumption, which is much appreciated.
Q: Did Naigai Vicars provide any new ideas, recommendations, or advice at the onset of the project?
A: The characteristics of our products could be defined as "biscuit snacks". We intentionally bake lighter products and biscuits. Typical biscuits melt slowly in one’s mouth; but our products melt rather quickly. Therefore, we asked Naigai Vicars to enhance the thermal insulation effect greater than usual in order to bake products in the first zone of the oven at higher temperatures than normal. This customization required extra insulation.
Sales engineers of Naigai Vicars are very knowledgeable about our company as they have worked with us for a long time, understanding our machines and equipment very thoroughly. Consequently, conversations for the customization discussions proceeded very smoothly. Naigai Vicars' ovens are made-to-order for our product and the ease of use is another reason for us to select Naigai Vicars to be our supplier.
Q: What were the reasons why you required a higher thermal insulation effect?
A: The reason was to conserve energy and minimize negative impacts to the environment. Since it is inevitable that heat will escape from ovens, Naigai Vicars designed an oven that would minimize heat loss during production by enhancing the thermal insulation effect.
If the insulation is insufficient, heat from the ovens also affects the overall temperature within the factory building. Naturally, an increase in the ambient temperature of the factory also leads to an increased load on the air-conditioning equipment.
Therefore, after the first Naigai Vicars' oven was installed, and based on discussions to determine appropriate countermeasures with Naigai Vicars by measuring the factory’s interior walls’ temperatures, we installed the second Naigai Vicars' oven.
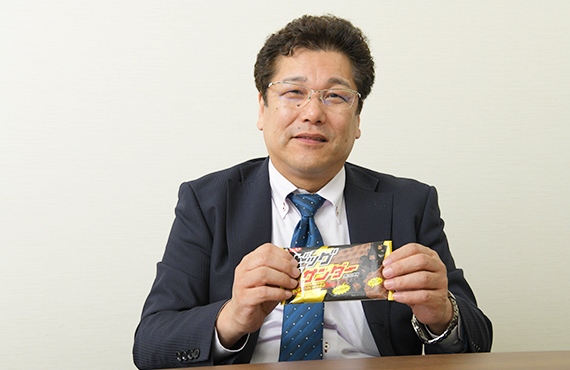
Maintenance leads to trouble prevention is much appreciated
Q: How would you rate Naigai Vicars’ maintenance?
A: We replace our ovens’ steel bands once every number of years. At a previous factory, I had experience dealing with another manufacturer that only replaced the steel band.
However, Naigai Vicars not only replaced the steel band; but also provided a comprehensive inspection, including an oven checkup, checking for any possible malfunctions and providing preventative care. Such service and care are provided during the band replacement, which we appreciate and are grateful for such advanced information regarding future maintenance.
Q: Have you ever had any big issues or problems?
A: We have been using Naigai Vicars’ ovens for 7 to 8 years with absolutely no troubles at all.
The other day, we actually had a little trouble with our overseas oven. The plastic resin gear portion of this valve that sends gas into the oven broke. It was surprising that such a piece would even chip and break as it did. Considering the maintenance aspects, there are definitely risks with overseas manufacturers.
Q: Please tell us about any future plans.
A: Beginning with greenhouse gas reduction, energy issues are now global matters. Being able to conserve energy and reduce the impact on the environment is a big challenge for us as well. Using ovens that are highly efficient and implement enhanced thermal insulation is one of the ways we can contribute to society.
I also am pleased that Naigai Vicars' burners are also well designed to increase their thermal efficiency. In the future, I look forward to other products that can further reduce the load on our entire plant, in addition to our ovens.
Q: Implementing energy-saving measures are big challenges even in our company. We will continue to work hard and strive to further improve this aspect of our operations.
A: Since ovens generate so much heat, including some exhaust, it is important to continuously think of measures to improve efficiencies. For example, it would be nice if exhaust heat could somehow be further circulated and used for something else. I heard of an example at a snowy factory, where exhaust heat is used to melt snow around the factory.
Though only conceptual at this point, we are wondering how we could generate warm water by using the excess exhaust heat from our ovens. Next time, together with the help of Naigai Vicars, we would like to make this concept into a reality.
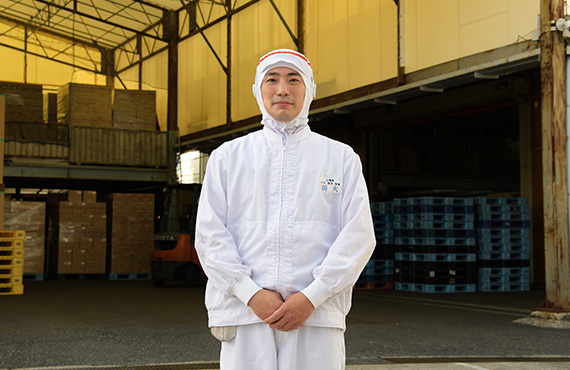
TAKARA SEIKA CO., LTD.
Yokohama Factory
First installed oven by Naigai Vicars still operational.
Quality & Maintenance that set us apart from others
Takara Seika Co., Ltd. founded in 1946, is a long-established confectionery company that makes biscuits and we have had a relationship with them since the establishment of Naigai Vicars. Three Naigai Vicars' tunnel ovens are currently in use at their Yokohama Factory. Mr. Nemoto, Yokohama Factory Manager, shares his views and evaluation on the usability and quality of Naigai Vicars' products and services.
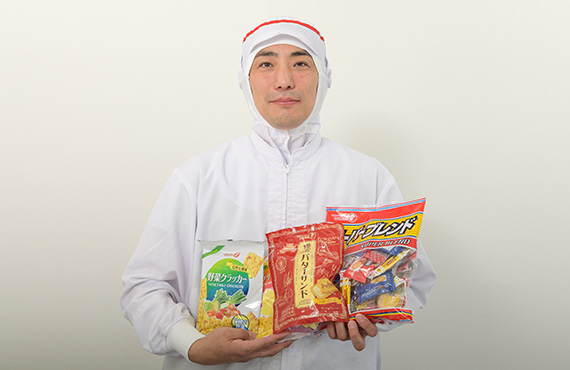
Over 40 years working together. In our company, when we refer to ovens, we mean Naigai Vicars' ovens.
Q: What kinds of products are produced here at the Yokohama Factory?
A: We have a brand called New Hi-Mix, and also produce cream sandwich biscuits which have cream in the middle. We produce roughly 20-30 tons a day.
Q: Are Naigai Vicars' ovens used to bake these products?
A: Yes, we currently have three Naigai Vicars' ovens.
The No.1 oven is 43m in length and uses a heavy mesh band, while the No.2 oven, 50m in length, uses a light mesh band, and the No.3 oven, which is 45m in length, also uses a light mesh band. The widths of the No.1 and No.2 ovens are 800mm and the No.3 oven is 1,000mm wide.
Q: How did everything get started between the two companies?
A: I heard that the relationship with Naigai Vicars started over 40 years ago. At that time, we had an electric oven, but we decided to change it to a gas oven, so Naigai Vicars' ovens were installed.
In fact, the oven that was first installed back then is still working now, the first Naigai Vicars' oven.
Q: Amazing. What were the reasons to switch from an electric to a gas oven?
A: First, we wanted to flame bake. Secondly, gas is more cost-effective and energy-saving than electric. Since then, when we refer to any sort of ovens in our company, we mean Naigai Vicars' ovens.
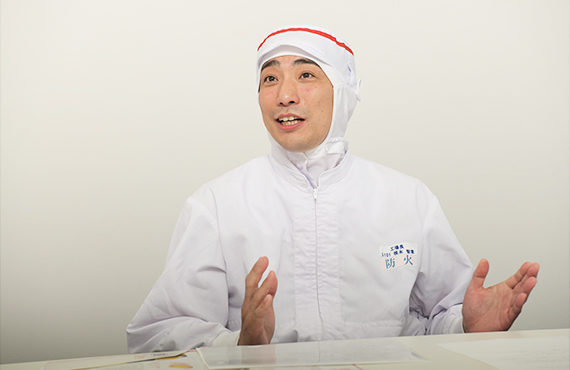
Naigai Vicar's ovens play a major role in the flavor of Takara Seika products.
Q: How do you maintain ovens that have been used for over 40 years?
A: As our company cannot handle the maintenance of our ovens ourselves, we recently asked Naigai Vicars for support in carrying out a large-scale, extensive maintenance of our equipment.
Our former president said "Because our products’ taste will change when an oven changes, we must be very cautious." He also said "The taste and flavor of our biscuits is based on our existing ovens", so I think that many employees have an attachment to Naigai Vicars' ovens.
Q: What an honor. One can feel and get a sense of history through this story.
A: As the people who handle the ovens and equipment changes over time, it is important to pass this history down. Even though basic operations are teachable and somewhat easily transferrable, it is rather difficult to teach sensory skills and techniques such as heat adjustment, which cannot be transferred via a manual. For such matters, this requires our staff to learn these skills and remember them by repetition and daily experience. To this end, we greatly appreciate the excellent, detailed, and thorough maintenance service of Naigai Vicars.
Q: You mentioned that the ovens recently underwent a major maintenance. How did it go?
A: Some repairs were needed in the electrical system. Regarding electrical defects, one defect might lead to another defect, so we decided to proceed while consulting with Naigai Vicars. The maintenance went smoothly thanks to following a scheduled plan created by Naigai Vicars.
Q: What kind of defects existed?
A: For example, there is a device to check the exhaust condition; which up until now, was managed by various people with each person handling it in their own way, which resulted in an inefficient operation. This time, we were able to improve the efficiency thanks to Naigai Vicars' supervision, management, and support. Naigai Vicars has vast knowledge and experience so they have handled various cases for us.
Q: As the ovens have been used for 40 years, wasn’t maintenance difficult?
A: It would have been better if we have had regularly maintained our equipment, but we had not for a while. Consequently, as ovens aged, some bugs and malfunctions began to appear. To fix everything at once is difficult, so we prioritized our repairs beginning with any safety-related malfunctioning parts or bugs.
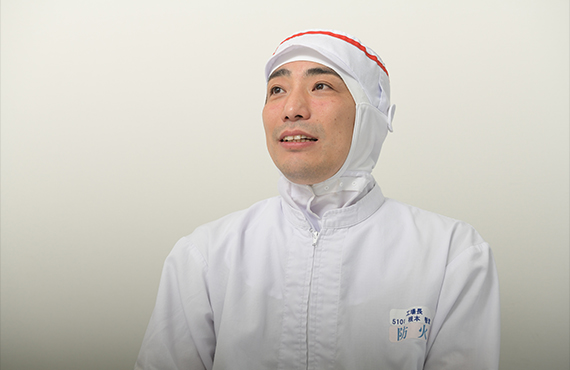
Delivering accurate and dependable maintenance services
Q: How does Naigai Vicars service compare to others?
A: Since Naigai Vicars has a deep understanding of and is very familiar with our company, we have a trusted relationship that allows us to easily contact them. When something happens, we can simply call explain to them by phone sometimes and Naigai Vicars will be familiar and understand the issue we are referring to.
Also, they provide us with frank advice such as, "If you repair this, you should repair this as well". It would be a waste to repeatedly make the same repairs that were already done previously. If there is a need for repairs, Naigai Vicars has such a wealth of knowledge and given their familiarity with our company, they suggest an overall economically efficient maintenance plan that takes our circumstances into consideration.
Q: Have you ever had any problems such as the need to stop the production line?
A: Never. They always consider our schedule and are able to complete the repairs etc. over the weekends.
Other manufacturers only send us quotations, whereas Naigai Vicars’ sales engineers physically come to explain the quotation in person. Since we are able to talk directly, we feel very secure and are extremely grateful. Naigai Vicars' customer service is excellent and frankly no comparison to other equipment manufacturers.
Q: Finally, please let us know if you have any future requests.
A: We do have plans to eventually replace our ovens. Since all of the ovens cannot be replaced all at once, proper planning and scheduling will be essential. I think for us, it will be important at that time to carefully manage the balance between the new and existing ovens. We will need to understand and optimize what we will be able to do with a new oven along with our existing ovens. We would like to plan and discuss this with Naigai Vicars.
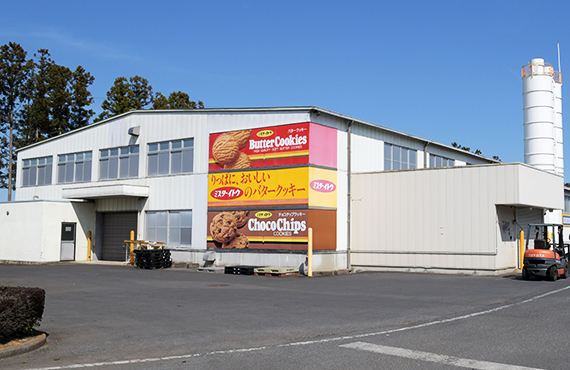
ITO BISCUITS CO., LTD.
We greatly value the speedy maintenance of Naigai Vicars and their highly productive, labor-saving confectionery production lines.
Ito Biscuits Co., Ltd. has been using Naigai Vicars' ovens for a long time. Mr. Iida of factory #1, Mr. Nesaki and Mr. Shimizu from factory #2, both shared with us about Naigai Vicars' ovens’ usability, reliability, and customer service.
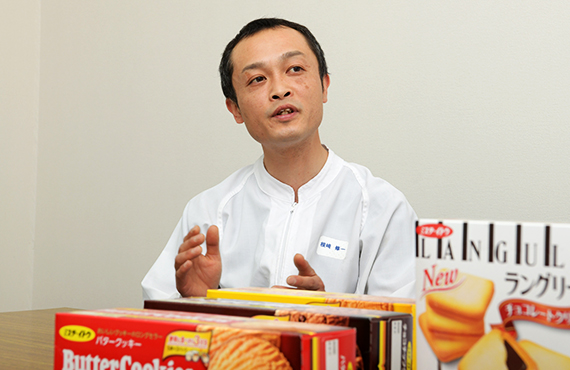
Tunnel ovens that support specialized manufacturers of cookies and biscuits
Q: Ito Biscuits Co., Ltd. have been producing high-quality products since their establishment.
A: We are a specialized manufacturer of cookies and biscuits founded in 1952.
In fact, Japan is the only country that distinguishes cookies from biscuits. In the US, it is called as a cookie, while in Europe it is called a biscuit. In Japan, if the total content of sugar and fat is 40% or more, it is defined as a cookie. On the other hand, if the total content of sugar and fat is less than 40%, the product is called a biscuit.
Our company specializes in the production of cookies and biscuits, and has been offering products that have been loved for a long time by everyone. And Naigai Vicars' tunnel ovens bear a significant part of our company’s production lines.
Q: In which process do you use Naigai Vicars' ovens?
A: The manufacturing process of cookies and biscuits begins with compounding (preparation), followed by mixing, then molding, and finally the baking process. Naigai Vicars' ovens are used in the baking process to both remove moisture and to add a baked color for each product.
Our products include both a dried type as well as a so-called flame-baked type, and since Naigai Vicars' ovens’ heat source is gas with flames, it is easy to add a baked color to the biscuits and cookies. In addition, because the thermal power is sufficiently secured, the production speed is both fast and very efficient.
Until several decades ago, we used to use an electric oven; but, then we installed a Naigai Vicars' gas oven to our new production line, which greatly increased productivity. Since then, we have relied on Naigai Vicars' gas oven.
Q: Do you mean that Naigai Vicars' oven is the best oven to use in order to maintain your products’ quality?
A: Yes, exactly. It has been a long time since we started using Naigai Vicars' ovens. They are indispensable for meeting the requirements of our products’ concepts and maintaining a consistent quality.

Excellent after-sales service. Naigai Vicars responds immediately to sudden repair needs.
Q: Are there any other merits to using Naigai Vicars as your supplier apart from their quality?
A: Previously, we integrated two ovens at our factory #1 into one oven, which I think was possible due to the high productivity of Naigai Vicars' oven.
Q: Did you need to bake the same production volume of two ovens into only one oven?
A: Yes, that’s right. As a result, it was also possible to reduce the number of personnel required to operate the oven(s), so even our human resources benefitted from more streamlined operations.
Q: I understand that your operations became more efficient in terms of human resources. How about regarding after-sales service?
A: Whether we would like to add some new feature or modification, or if one of our ovens requires some urgent repairs, Naigai Vicars responds immediately. For example, if I contacted Naigai Vicars to fix something, they would come to our factory on the same day. What would usually take about a month to repair or resolve from the beginning to the end, Naigai Vicars has completed in two weeks. Even when there have been problems in the past that required some repairs, we have not once had to stop or interrupt our production.
There are a variety of services out there; but, for us, immediate action is most appreciated. We used to use overseas oven manufacturers, but the after-sales service quality and level of Naigai Vicars is no comparison. We are also satisfied with cost. We also appreciate the fact that Naigai Vicars is always sincere and earnest even when we sometimes make unreasonable or extremely difficult requests.
Q: Compared to overseas manufacturers, are there any other differences other than Naigai Vicars’ customer service?
A: When we used to use overseas products, small things often gave us stress. For example, we can handle small problems on our own, but overseas products are manufactured differently. For example, for any screws that need to be used horizontally, on the side of a piece of equipment, overseas manufacturers often use negative screw heads (while Japanese manufacturers would use a positive screw head to lessen the chance of the screw to fall). There have been cases where we wished a positive screw head was used instead of a negative one.
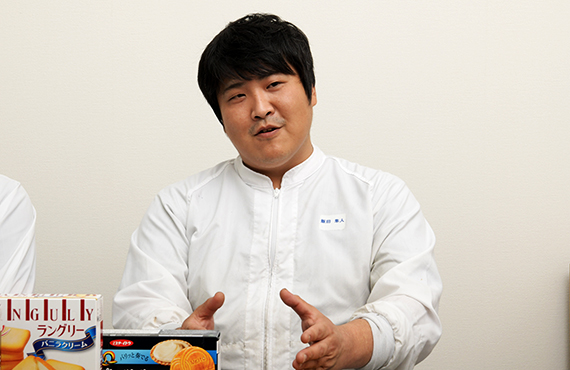
Maintenance services are excellent while maintenance instruction manuals and information are also very helpful
Q: Did you have any major problems or issues once you started using Naigai Vicars' ovens?
A: Previously, the oven burner had caused incomplete combustion to occur. The reason was not due to Naigai Vicars' products, but rather our lack of thorough daily maintenance.
When we consulted Naigai Vicars about this matter, they kindly responded to our burner repair requests despite the lack of attention on our side. In addition, we received advice and lectures on maintenance and other technical aspects, which led to an improvement in the overall level of workers in our factory. I feel that Naigai Vicars has always offered such additional benefits and extras to us.
Q: How easy has your daily maintenance become now that you use Naigai Vicars?
A: We use three types of oven bands / belts: steel, light mesh, and heavy mesh. Cookies are baked using steel bands, while biscuits and crackers are baked over a strong flame using mesh bands with a short baking time. By using bands properly, the range of our our product lineup has expanded, but at the same time maintenance has become more complicated. Naigai Vicars’ maintenance service support has also been substantial in this regard.
The other day, I asked a Naigai Vicars' sales engineer how to remove charred parts on the equipment, and he kindly taught me about the maintenance cycle as well as provided me very helpful information on cleaning tools we can use. A few years ago, prior to conducting our own in-house training for our factory workers, I was able to take a class at Naigai Vicars. I am appreciative that they offer such courses and opportunities.

New product development to meet contemporary, premium sweets demands for adults
Q: What are the product trends in recent years from the perspective of Ito Biscuits Co., Ltd.?
A: There are needs of the times. We started with simple biscuits, next we needed to increase our lineup of biscuits that used butter and/or chocolate chips, followed by increased demand for cookies, and then the shift in the overall proportion of cookies and biscuits changing further, with cookies then surpassing that of biscuits.
Recently, however, there is even a newer genre of sweets that is not characterized into the cookies or biscuits category. It is often referred to as an “elaborately baked confectionery”, but the actual product category type listed on the package is called “baked confectionery”.
Q: Are the raw materials different?
A: The basic raw materials such as wheat, fats and oils are the same, but the wheat and fats are of higher quality, and the end products are more sophisticated.
Q: Do you mean to say that the quality, complexity, and sophistication of confectionery products overall has increased?
A: That's right. Trends include more premium products for adults, with individual packaging for each product. For example, there is a product called a pretzel. Originally a German snack, it is string-like dough product shaped into a loose knot.
We offer a product called “Pretzel Sand Classic Vanilla”. The pretzel dough is reproduced and baked into a thin biscuit shape with cream sandwiched in the middle, but it is difficult to bake. Naigai Vicars’ oven is also indispensible here.
Q: Customer needs are changing with the declining birthrate.
A: Yes. Recently, in the biscuits and cookies market, the population that eats biscuits is decreasing due to the aging of our target customers. Consequently we have to offer new products. Some of our products include a dough base that is baked about 40 minutes, then topped with sliced almonds and baked further, but this is very difficult. For such products, we also received advice from the "baking professionals", Naigai Vicars. Thanks to their support, we are able to bake and handle such new products.
Furthermore, as recent products require very high quality standards, we would like to improve productivity while consulting and receiving advice on such points.
Q: Any requests to Naigai Vicars?
A: The tunnel ovens installed in our factory are designed for mass production of the same product. The existing ovens are good at baking one product in large quantities, but customers are demanding assorted packaging; so if possible, it would be nice if two or three different kinds of products could be baked at the same time in one oven. For Naigai Vicars' burners, there are three-section burners that can be divided into three flame outlets and set the flame intensity set to five patterns, but we would like an oven that can bake in three different temperatures at the same time.
Recently in the biscuits market, our target customers are getting older and the population that consumes biscuits is decreasing. We would like to ask Naigai Vicars to build ovens that match our customer’s needs.
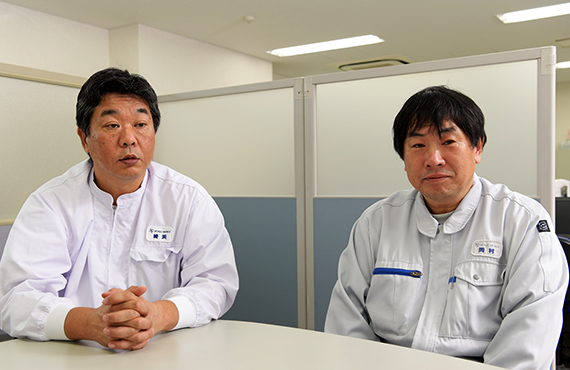
YOKU MOKU CREA CO., LTD.
Consulted Naigai Vicars when developing a new product.
Resulting in a delicate dough baked into a smash product
Yoku Moku Crea Co., Ltd. is in charge of Yoku Moku Group's manufacturing department. We have our Nikko Main Factory, Kanuma Factory and Tokyo Factory, with five Naigai Vicars' ovens in the Nikko Factory and another in the Tokyo Factory. Our main product "Cigare", is baked by a specially customized Naigai Vicars’ oven. We interviewed Mr. Sakihama, General Manager of the Production Technology Department, and Mr. Okamura, Equipment Section of Nikko Factory to learn about the early days of the relationship and some of the details behind the various installations.
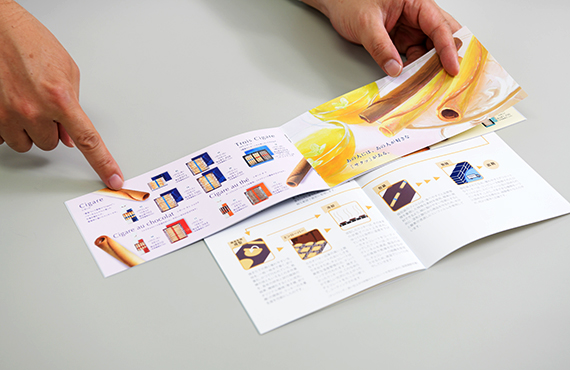
Consulted Naigai Vicars for the development of our main product, through which they customized the ovens to match our particular needs.
Q: Yoku Moku Crea Co., Ltd. manages and operates the Nikko Factory, Kanuma Factory, and Tokyo Factory, doesn’t it?
A: Yes, both our headquarters function and main factory are at one single location here in Nikko. We also have the Kanuma Factory in Tochigi Prefecture as well as our Tokyo Factory in Umejima, Tokyo. There are five Naigai Vicars' ovens in the Nikko Factory and one in our Tokyo Factory. Before our Nikko factory was built, we used to have our Imaichi Factory, which deteriorated and became unusable.
Q: You have installed many Naigai Vicars' ovens. What was the catalyst or genesis to start using their ovens?
A: One of our main products is a long-selling cookie called "Cigare"; and when we started selling this product at department stores like Mitsukoshi and Isetan, there were long lines of customers from the morning. "Cigare" were initially baked using deck ovens, but as growth in demand led to the need for mass-production, we installed a tunnel oven. It was during this time that we consulted Naigai Vicars, and they provided various solutions, from changing the position of burners and adjusting the air supply and exhaust amounts according to our requirements, to adjustments that would reflect our desired product taste, baked color, and texture, etc.
Q: Did you implement a specialized Naigai Vicars’ oven for "Cigare"?
A: As "Cigare" is a langue de chat dough cookie, I believe that only a specialized oven that has repeatedly been fine-tuned could produce the unique doneness required.
Our past-president at the time of Nikko Factory built also said, “Cigare cannot be baked easily, we require an oven that has the know-how cultivated with Yoku Moku in the past.”
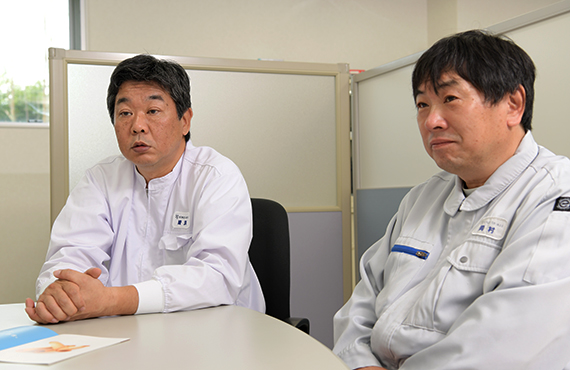
We highly rate the know-how and technology of Naigai Vicars' ovens that have maintained a high quality for over 40 years.
Q: What do you think about the usability of Naigai Vicars' products compared to other companies?
A: Compared to other companies, Naigai Vicars' ovens are able to manufacture high quality products for a long time, which makes them very reliable.
Our products’ dough is very delicate, so it’s not like our products can easily be reproduced in a microwave oven by simply adjusting the kilowatts settings and such. Rather, I think because we have been able to share our respective technology and know-how with each other for over 40 years, we have been able to manufacture and maintain high quality products.
Q: Have you ever had any issues or challenges when you were installing any of the ovens?
A: When we built the Nikko factory, we thought it would be pointless to select an oven manufacturer without the proper know-how and expertise. Consequently, we asked Naigai Vicars to manufacture an oven at their Kawaguchi Factory. During the manufacturing process, various members of our staff in charge of dough and oven operations were onsite to verify and validate both the equipment and manufacturing of our Yoku Moku products.
Both companies repeatedly tested, adjusted, and fine-tuned the oven’s intake and exhaust systems and burner controls, etc.. For any of the adjustments, we continually used trial-and-error until each system or control was perfect. We even repeated numerous tests and trials even during our hot summer season to figure out the best settings to bake stable dough, paying careful attention to the room and steel band temperatures, for example.
We believe that our existing ovens are indeed specialized, customized, original, ovens that successfully integrated all of our expertise and has taken into consideration the various ways we can and would like to bake our products.
Q: How does Naigai Vicars respond when any issues would arise?
A: The engineer who takes care of our company has been involved since our very first oven installation and knows us very well, so we can often receive support and various advice over the phone.
There are other manufacturers who when we call for just a little bit of advice, are very slow in their responses and their actions are delayed and/or take a long time. On the other hand, Naigai Vicars responds at once and we are grateful that they promptly come up with solutions and deliver them straight away. There has never been a major problem, and if there ever was an emergency, they would respond immediately.
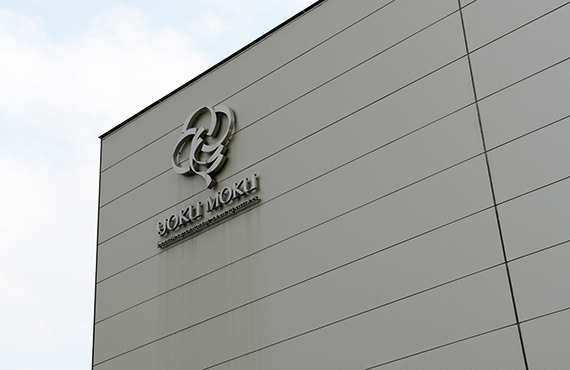
When the Naigai Vicars' ovens were installed at our Nikko Factory, we requested countermeasures to prevent against power failures caused by lightning.
Q: How is Naigai Vicars’ maintenance?
A: Here in Nikko we experience large seasonal variations, so frequent and often times very minor adjustments are necessary because of the cold or hot weather, and/or high humidity which all somehow affects the ovens’ conditions. Also, when seasons change, the gas mixing ratio also changes due to fluctuations in atmospheric pressure, so this also requires some fine adjustments to the oven’s operating systems and controls.
Q: I see. You need to make various adjustments according to the environment. How drastically does the environment change?
A: Yes. In this area, the outside temperature rises to +30 ° C or higher in the summer and drops to around -10 ° C in the winter. In addition to changes in the environment, the North Kanto region is also said to be in the “path of lightning”, and our Nikko Factory is also located along this potential lightning path. In fact, a sudden power outage caused by lightning fall is serious and would be detrimental to our business. If our 27-meter-long tunnel oven stopped running due to a momentary power outage, all the products in the oven baking chamber at that time will need to be disposed of.
Q: That is serious. Have you any countermeasures?
A: The ovens in our Nikko Factory were customized not to stop during a momentary power outage due to lightning. We are now safe thanks to a backup system. We didn't have this while we were at our Imaichi factory, so lightning caused stoppages and resulted in unstable operating conditions.
Q: Do you have any future requests to Naigai Vicars?
A: I would like to save more labor for our oven operators. In order to properly maintain the quality of products, not only is our oven performance important, but so are our human eyes. Currently, an oven operator is monitoring and adjusting the burners to control the temperature so the products’ baked color is according to specifications. If we were able to manage/control this automatically, this would equate to a tremendous labor saving.
The current situation everywhere is that the succession of technology is very difficult due to the lack of capable human resources. This is why I think equipment and machines these days have to compensate and alleviate our human resources burden and lack thereof more than ever. I hope such a solution can be provided.
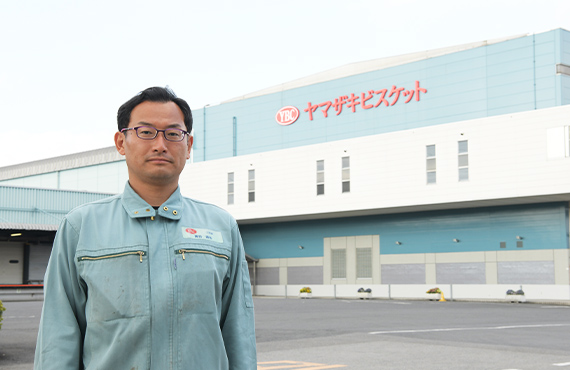
YAMAZAKI BISCUITS CO.,LTD.
Koga Plant
From Installation to Maintenance and Air-Conditioning Consultation.
Reliable partner with continuous support and technical capabilities
Yamazaki Biscuit Co., Ltd. changed its name in September 2016. The company manufactures a variety of snacks and biscuits, including the long-selling Chip Star and Levain series. The products have been a favorite of customers for many years, and Naigai Vicars' confectionery baking processing equipment have been used throughout. The following content is based on an interview with the engineering manager at their Koga plant for this case.
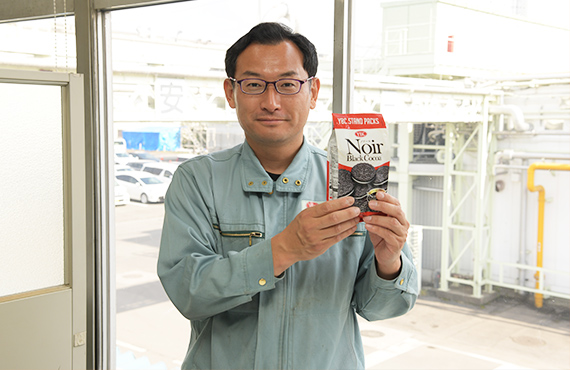
Because a trusted relationship has been built up, it went without saying to consult Naigai Vicars (for our manufacturing plant).
Q: What are the main products of this plant?
A: We produce the Levain crackers series, both Chip Star and Aerial brands within the snacks portfolio, Noir within biscuits, and so on. As an aside, Levain means "leaven" in French.
Q: How are Naigai Vicars' products used at Yamazaki Biscuits?
A: We have been dealing with Naigai Vicars for many years. The relationship started from before I joined the company. So for me, Naigai Vicars' products and services feel like as if they are "always here".
Naigai Vicars' products are mainly incorporated into our baking and frying processes for our products in this plant.
Q: Can you please share the reasons for this ongoing relationship?
A: The basis of our highly trusted relationship has been built on successful past results. To do with our ovens or fryers or any other related matter, we have a sense of security that we can fully rely on Naigai Vicars and can consult with them on basically anything plant-related. Naigai Vicars is indispensable to our company.
Q: How do you value and rate Naigai Vicars' products and capabilities compared to other company’s products and services?
A: Naigai Vicars is very familiar with our specifications. Accordingly, Naigai Vicars provides the most attentive and best overall service for us from installation to maintenance of our equipment.
In addition, Naigai Vicars not only make suggestions unilaterally, but they also make proposals reflecting our opinions from the factory floor, so we can develop the most suitable solution for us. Consequently, we hear of no issues from our plant operators, which further strengthens our already trusted relationship.
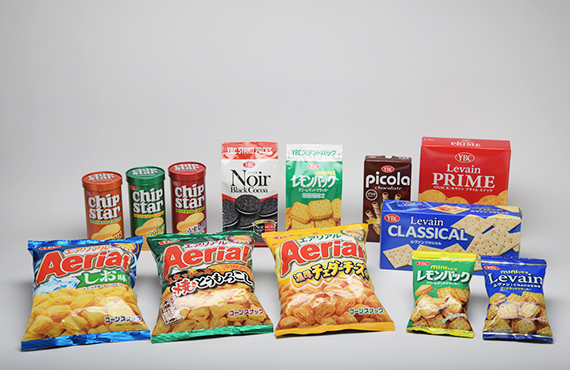
Upgrade from manual to automatic ignition system success story. Large contribution to efficiency
Q: Can you provide any specific examples?
A: Naigai Vicars upgraded our ignition process to an automatic ignition system. There are hundreds of burners on an oven, and previously gas burner knobs (cocks) were opened manually. Now this igniting process has been automated. This upgrade has led to shorter start-up times and improved our efficiency.
Q: How is the maintenance quality?
A: Pre-planning is very good. There is a saying that 80% of our work is proper planning, and thanks to Naigai Vicars' organization, proper planning, arrangement, and preparation, our actual working time is shortened.
Burner maintenance and repairs of our ovens are conducted once every ten years. Naigai Vicars completes this maintenance a day or two before the actual maintenance deadline. If this were left to the last-minute, and any irregular conditions arose, this would cause a significant issue for us, so we greatly appreciate their speedy maintenance service leaving time to spare. Thanks to no accidents or incidents, we are able to operate safely each and every day.
Q: Do you have any specific stories you can share with us regarding maintenance?
A: We actually operate long length band ovens, and one day, a large cylinder that pulls the band broke.
The issue would have taken us days to replace the part to solve the problem. Thankfully, Naigai Vicars suggested a first-aid solution based on a similar case that occurred at another company they serviced in the past. Until the replacement part came, we were able to manage the situation thanks to Naigai Vicars timely support.
Q: How about other manufacturers maintenance?
A: The impression is that there is limited to no adaptability or flexibility for irregular matters or issues that arise periodically. Even for a simple matter, they typically respond by stating that this issue is "outside of our quotation or service", is too difficult to deal with, and they are very rigid on their servicing time. However, Naigai Vicars’ engineers will continue working until the issue is completely and satisfactorily resolved, not based simply on serviced hours. I believe that Naigai Vicars can do this because they also have the technical capabilities.
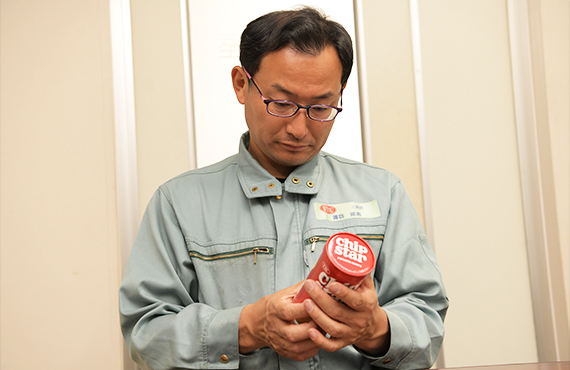
As well as maintenance, the announcement of product information is also appropriate
Q: Have you ever had any trouble or issues with your equipment?
A: Our experience with other manufacturers is that they tend to be inadequate in sharing timely information with us such as a potential parts shortage or production equipment discontinuation.
On the other hand, Naigai Vicars announces and informs us not only of future potential production equipment or parts discontinuation, but also provides with what will be necessary for the next generation or successive model, so we can be at ease and not be stressed with the transition.
Q: How is Naigai Vicars with regards to energy-saving and environmental measures?
A: Energy-saving is a universal goal, and we always take this into consideration when introducing a new piece of equipment or solution for us.
We have a process requires the use of steam, which in the summer, significantly increases the room temperature, so we consulted with Naigai Vicars. They were able to provide a solution by creating wind flow, which improved the balance between air inflow and outflow, thereby reducing the interior temperature of the room.
Q: Sounds like that Naigai Vicars is also able to support and provide industrial air-conditioning solutions as well.
A: We consult Naigai Vicars on various matters. As mentioned earlier, the existence of Naigai Vicars' is indispensable for us. However, we also realize that there is likely a significant amount of work and effort being conducted in the background, unknown to us. Consequently, we presume that Naigai Vicars is then able to provide various solutions for both equipment and operational improvements very efficiently and make our tasks such as daily maintenance very easy for us to do.
Q: How would you describe or summarize Naigai Vicars as they relate to your company?
A: Baking equipment and industrial air-conditioning system experts. That is our impression. So if there was any project or matter that related those, we would naturally consult with Naigai Vicars.
Q: Any requests to Naigai Vicars?
A: In my opinion, if possible, I would like to manage our equipment remotely, using technologies such as IoT and AI. For example, if it were possible to use machines to manage equipment as well as parts that were difficult to reach or see with human eyes or hands, not only would efficiency, but also safety improve, thereby reducing potential accidents.
Q: Going forward, sounds like you will continue to request Naigai Vicars to assist you with product development?
A: Yes, of course. If we are to start any new product or project, for example, in order to develop a new texture, we would need to remodel our ovens and/or fryers. I am convinced that Naigai Vicars will be involved with us throughout the process on through to completion.